Features & Models
EJECTORS
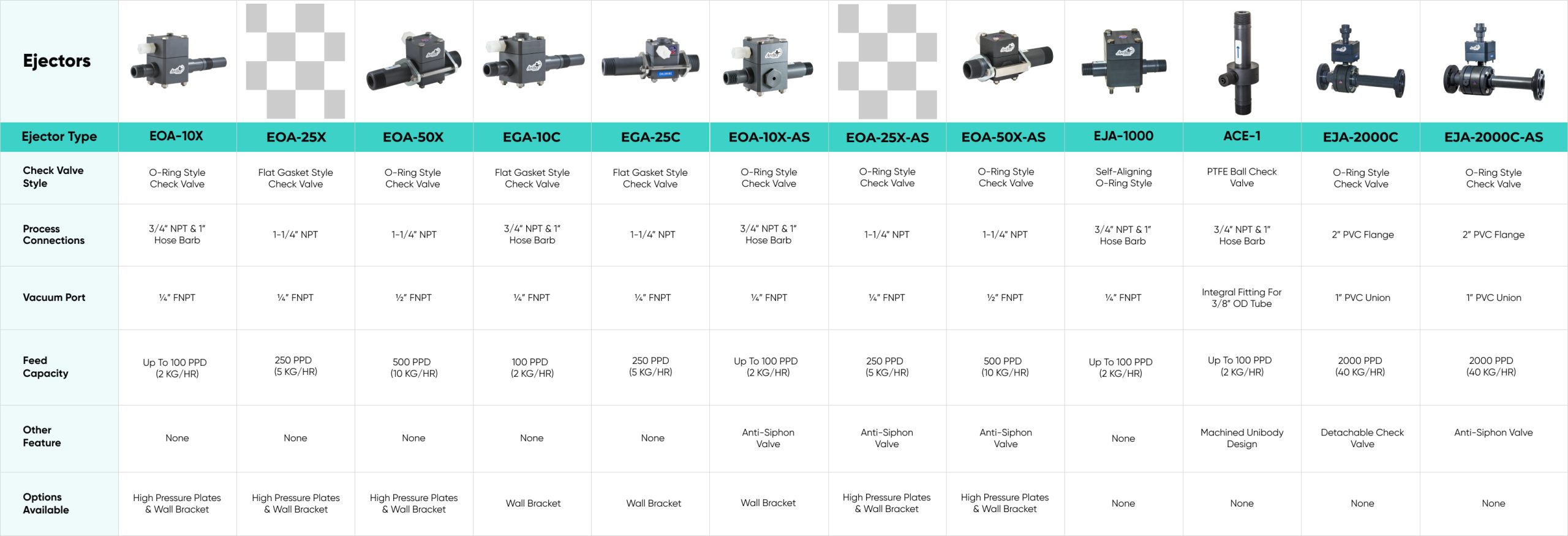
Every Archer Instruments Ejector is manufactured using all machined parts. No parts are injection molded. Only the best materials are used for each part.
Archer Instruments manufactures Ejectors for gas feed capacities (for chlorine or sulfur dioxide gases) as low as four pounds per day (seventy-five grams per hour) and as high as two thousand pounds per day (forty kilograms per hour). Gas feed capacities for ammonia gas are offered as low as twelve pounds per day and as high as two hundred fifty pounds per day.
The Archer Instruments line of Ejectors includes a variety of designs. The primary differences between the different models manufactured by Archer Instruments are related to the design of the internal check valve and to the size of the Ejector assembly. With the exception of the model ACE-1 Ejector, all Archer Instruments ejectors incorporate a diaphragm type spring-loaded check valve. The ACE-1 “Compact Ejector” is designed with an internal spring-loaded ball check valve.
The following information is specific to the feed rates of Chlorine or Sulfur Dioxide gases only. For applications involving other gases please consult the factory.
Model ACE-1 – For feed rates of up to 100 PPD (2 kg/hr). Process connections ¾” male NPT or 1” I.D. hose
Model EJA-1000C – For feed rates of up to 100 PPD (2 kg/hr). Process connections ¾” male NPT or 1” I.D. hose (inlet only)
Model EOA-10C – For feed rates of up to 100 PPD (2 kg/hr). Process connections ¾” male NPT or 1” I.D. hose
Model EGA-10C – For feed rates of up to 100 PPD (2 kg/hr). Process connections ¾” male NPT or 1” I.D. hose
Model EOA-25C – For feed rates of up to 250 PPD (5 kg/hr). Process connections 1-1/4” male NPT
Model EGA-25C – For feed rates of up to 250 PPD (5 kg/hr). Process connections 1-1/4” male NPT
Model EOA-50C – For feed rates of up to 500 PPD (10 kg/hr). Process connections 1-1/4” male NPT
Model EJA-2000C – For feed rates up to 2,000 PPD (40 kg/hr). Process Connections 2” Socket PVC Sch80 flange
The operation of the internal venturi nozzle requires that a motive water source supply a pressurized flow that exceeds a minimum requirement specific to both (a) the system backpressure into which the Ejector will discharge and (b) the size of the nozzle being used. Each Archer Instruments Ejector is available with several different nozzle sizes. Hydraulic performance charts or tables are published in the Ejector manual, which provides detailed information about the supply water pressure and water flow necessary to operate each nozzle. Please consult the factory with any questions related to nozzle selection or the supply water hydraulic requirements of any nozzle.